The reasons of warpage in injection moulding
Warpage is usually caused by moulded-in stresses. The issue of warpage is related to being a semi crystalline material, HDPE, being semi crystalline polymer, will have differential shrinkage along and across the flow leading to warpage. It is difficult to eliminate this problem just by optimizing processing parameter. If use of multiple gates is possible, that might help multidirectional flow leading to lesser warpage.
The two areas that will have greatest affect are injection mould temperature and gating being both location and type. Not knowing configuration or flow difficult to give specific advice, but think of the part on a molecular scale. Imagine the surface of part being interconnected crystals with cooling starting at coldest surface of injection mould which will be multiple points and spreading out in a circular shape all within fractions of a second. You want the coldest surface possible and repeatable and a flow front that fills mould as evenly as possible. The more even the flow front in relation to part configuration from one side across to other and a Plastic Injection Mouldsurface temperature that is a uniform temperature will minimize warp. There are some design tricks that would also minimize warpage but you may past that point. As to type of gate, as large as possible so you are not adding heat through shear. Also monitor melt temp at nozzle, looking for lowest temp that will enable complete mould fill.
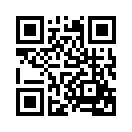
- Name:
- Mr.Zeng
- Tel:
86-571-86433485
86-137-32202800
86-189-58129996
- Email:
- sales@fridgtec.com
- WhatsApp:
- https://wa.me/8613732202800
- Skype:
- Skype:hzpkrichz
- Address:
- Rm 910, Baideli Bldg, No.519, Gonglian Rd,Binjiang, Hangzhou,China